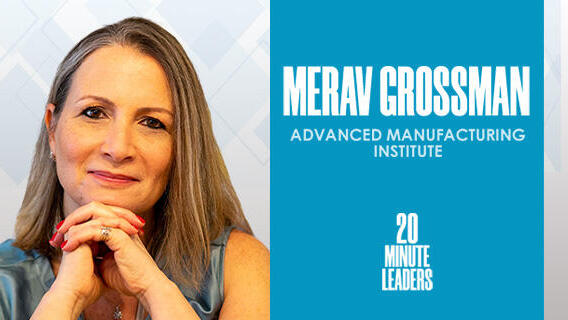
20-Minute Leaders
“Becoming an end-to-end smart factory is a journey.”
Helping industrial plants transform into advanced manufacturing centers that are part of industry 4.0 is a passion for Merav Grossman, CEO of Advanced Manufacturing Institute.
Helping industrial plants transform into advanced manufacturing centers that are part of industry 4.0 is a passion for Merav Grossman, CEO of Advanced Manufacturing Institute. She is excited to be part of creating better workplaces for employees and improving systems and processes. Grossman shares that becoming a fully digitized and smart factory is a journey that is accomplished through many small steps, and AMI helps companies all along the way. Though they focus on small to medium businesses, more large companies are coming to the institute for help. She explains that working with these more mature companies requires providing even more value. Throughout her career, she saw many different kinds of factories and realized that the challenges they face are very similar across different sectors. Grossman has used her technology background to lead changes in many places on her own journey and enjoys continuing to do so with AMI.
Click Here For More 20MinuteLeaders
Tell me about your career and what's been guiding you throughout your thinking process in your career.
I think that what was leading me all the time was something that will be very interesting for me and related to technology and improvement in some ways. I'm an information system engineer. I studied as an academic reserve. So I studied before the army. I served in a professional unit in information security back then. For about 12, 13 years, I focused mainly on information systems as a CIO in several organizations.
2001 was the first time I joined the industry. Before that I was in an academic institution and in a retail chain, so this was the first time I joined an industrial plant. I added some more areas like in supply chain, planning and logistics, and purchasing, et cetera, which was very much connected and based on my previous knowledge. It helped me lead the changes that I wanted to lead.
From 2007, I began my new journey in supply chain and later on in business development, until I even managed to lead a startup that was like a spinoff from this plant that focused on some niche product. Back then, it was in the glass industry, float glass industry. So this was a security glass. Later, I joined the medical device sector, which is again a big change, but in global supply chain leadership. I can tell you now that I already saw hundreds of plants. It's amazing how much similarity there is in the challenges across different sectors. I like to change. It's always in my life. I'm a person that likes to try things and learn all the time.
Tell me a little bit about industry 4.0. What does that mean to you and to AMI?
Today, I lead as a CEO at AMI, Advanced Manufacturing Institute. It's a national institute in Israel working under the Ministry of Economy and Industry. But it is a private company, which is owned by three entities: Tefen Management Consulting Group, one of the leading consulting groups in Israel; ESI, which is a software house with solutions in AI and big data; and Braude Academic College, which is an academic arm for us. We see ourselves as the main focal point for industrial plants, mainly traditional and SMBs, to lead them and support them in their journey towards advanced manufacturing or industry 4 in order to improve their productivity.
Sometimes people mix the two phrases: industry 4 and advanced manufacturing or smart factory. The reason to call it 4.0 is because we see it as the fourth industrial revolution. Industry 4.0 takes all the background of technology, automation and robotics, 3D printing, and of course the computers and internet, and enables a factory to become end-to-end digitalized. When you are looking at advanced manufacturing, you look throughout the life cycle of the product and the different areas of the plant and you expect them to be digital, to be integrated in between. You expect the managers or the organization to take decisions upon data to use all that technology has to offer so far. When you look at a traditional plant, usually it is a journey. It's not that you jump from your current situation to 4.0 or to being end-to-end a smart factory. We help them throughout this journey.
Tell me about the work that you do working with organizations that are making that transition and adapting to this new world. How does this collaboration happen?
We have a very methodological way to work. First, we go into the plant. We study it in the first phase in order to understand all the challenges in the different areas, all the opportunities that they have there in order to improve their processes and systems. Then we issue what we call a roadmap for being an advanced plant. Then we present the picture to the management. First of all, they need to realize what their situation is. They are also graded between one to five in several areas.
The second stage is we build, with them, a roadmap. A roadmap is the one pager. Pretty simple. We make them a list of projects that we think that if they follow, they will improve. After, they breathe a little bit and discuss it inside. After a short while, we follow up with them and then we begin the process of implementing the project. The Ministry of Economy is really supporting them with a significant budget depending on their size, et cetera. They also get our professional support. They get professional companies that we match to them to implement the project. We really have a very nice plan here.
Tell me about why you are so excited about this.
Every time that I come to a plant after a few months, or one year, and see the progress that they have gone through, it's really exciting. You really feel that you support and create a better work environment, better work experience for the employees. It's a great privilege and honor to be able to lead such an organization.
For example, a big wood processing firm made changes in the way their machinery is arranged and organized on the floor to create more productivity. They implemented a new application in their engineering team, one that has really improved and shortened the time to plan the project for the customer, first. And second, it was integrated directly into the machine. After a few months, they already made great progress, and we saw that they managed to define KPIs and dashboard for several areas in the company. Then after another period of time, they implemented the Monday application. They decided that every month or so, they define another improvement that they are going to do. It's really nice to see.
How does your day-to-day look?
My day-to-day consists of meeting with potential customers, many times. We are developing several courses. For example, we currently have a one big program that we call "innovation leaders." We are going to issue our fifth program. But we are now issuing a new educational program called "advanced manufacturing manager" with our colleagues in Braude Engineering College. I'm working a lot on marketing this program for industrial companies and my colleagues. We are running webinars every month, so I'm of course involved with that.
I'm now working on two very strategic projects. We are working on a physical experience center. It's already built. Now we are working on the content that we want to present there. The media and the digital means there will be very much sophisticated. For example, we are going to present a robotic assembly line to just describe the possibilities. We are calling technological companies to join us and to present the solution there in a partnership model.
The second one: So far, we were focused on small medium business because this is the mission from the Ministry of Economy. But big companies are contacting us more and more because we grew the awareness. It's a little bit of a different story because the bigger and the leading companies are much more mature and then you really have to bring them some more value. I'm working with Tefen Group on a combined program for this kind of company. We are collaborating with a German Institute there. This is something I'm really now cooking up.
Michael Matias, Forbes 30 Under 30, is a Venture Fellow at Innovation Endeavors as well as investment Venture Partner at Secret Chord and J-Ventures. He studies Artificial Intelligence and Human-Computer Interaction at Stanford University, and was an engineer at Hippo Insurance. Matias previously served as an officer in the 8200 unit. 20MinuteLeaders is a tech entrepreneurship interview series featuring one-on-one interviews with fascinating founders, innovators and thought leaders sharing their journeys and experiences.
Contributing editors: Michael Matias, Megan Ryan